Overview of
our services
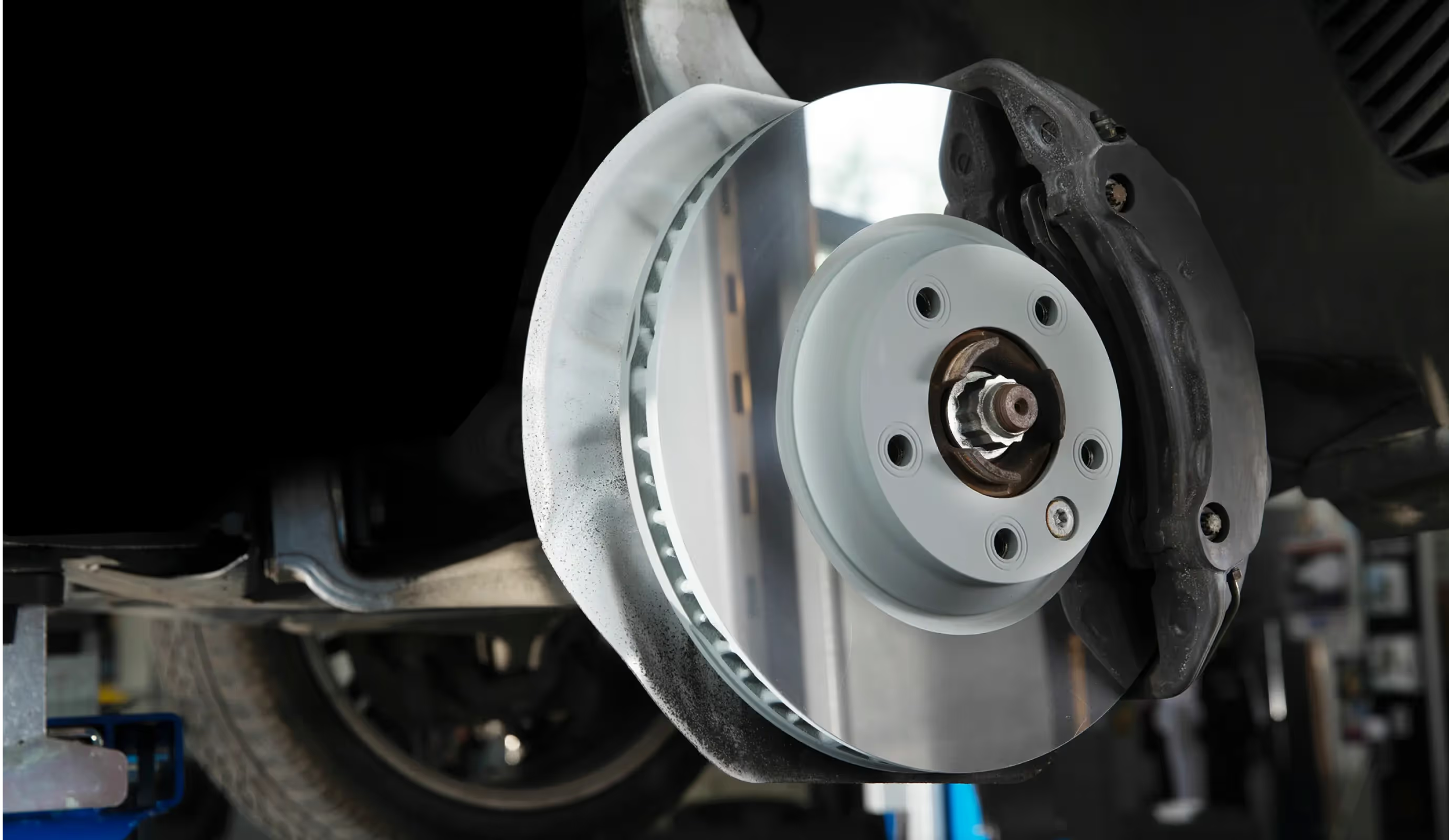
Breyden supports its customers from the initial idea to serial production. Discover our impressive range of services here.
Development
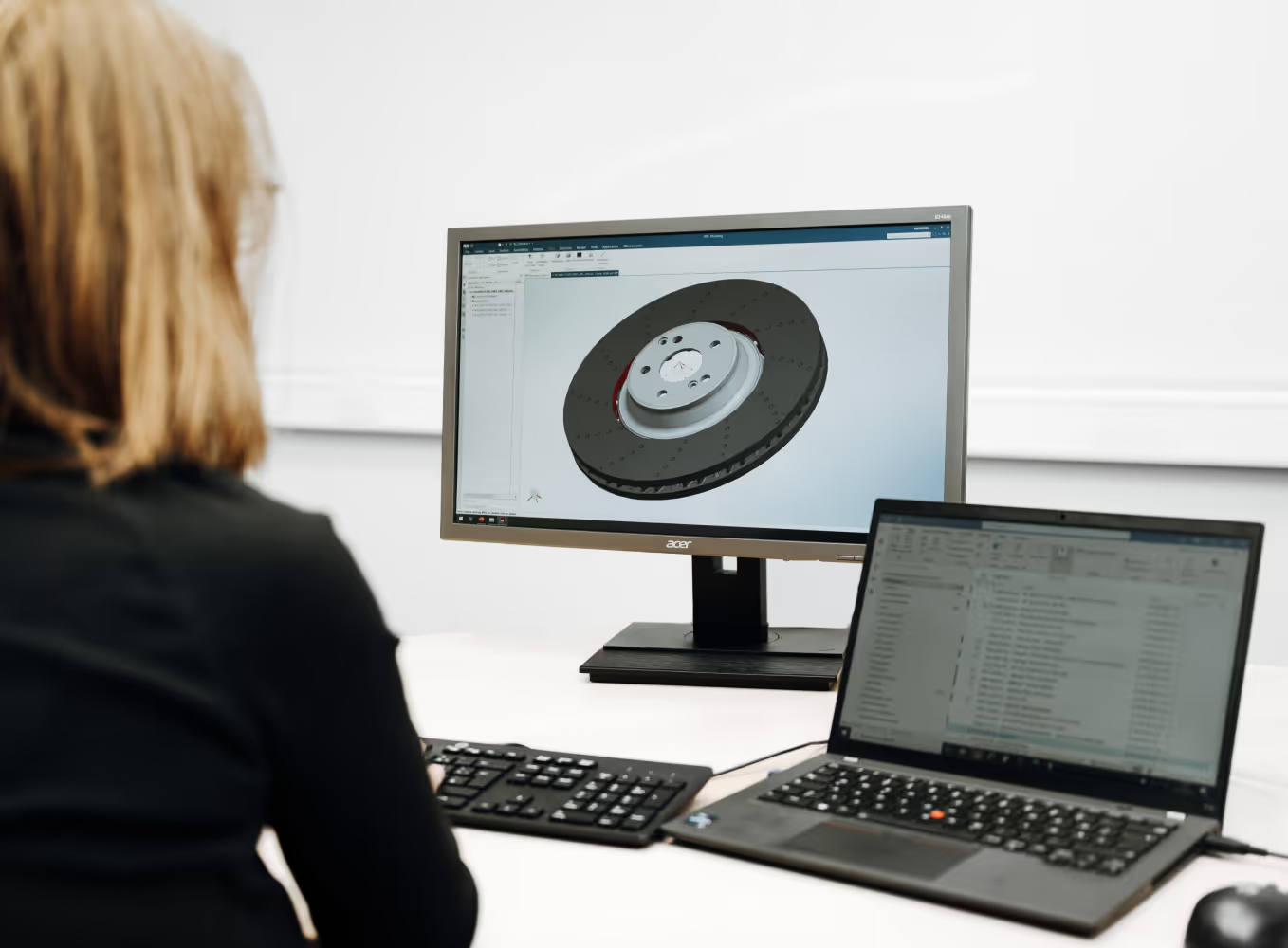
Engineering design
The foundation of product development
CAD design is an essential tool for us in the development of new products. Efficient implementation from the initial idea to the finished product is made possible by using Siemens NX and Catia V5 CAD systems. The use of these CAD systems facilitates interdisciplinary collaboration across different areas, helping to identify and resolve potential issues early. CAD design forms the basis for simulation and evaluation of the design before creating physical prototypes.
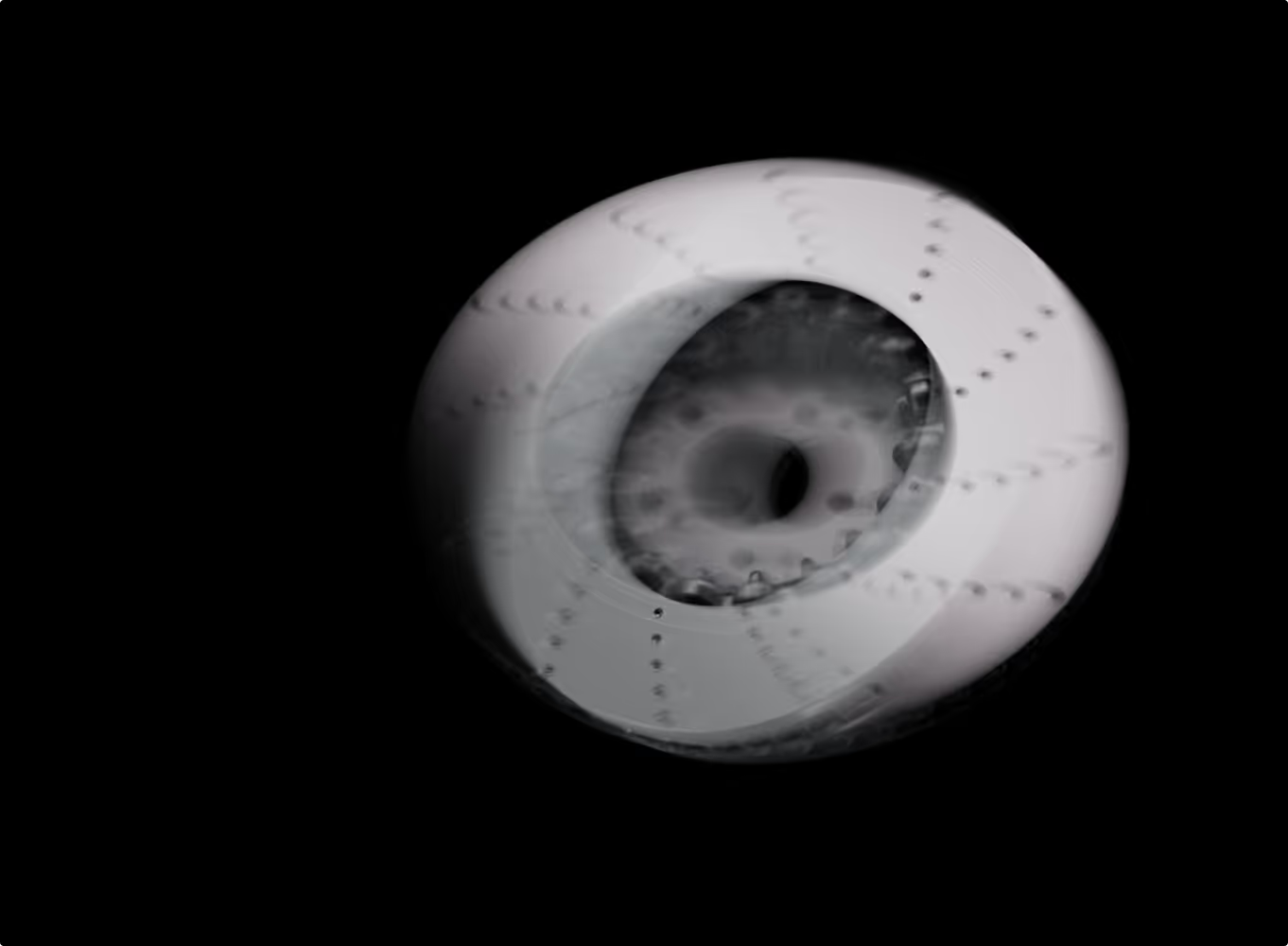
Simulation
For pioneering insights and evaluations
In our development process, we specifically rely on FEM (Finite Element Method) simulation as a key component. We use Abaqus and Altair software for this purpose. Our expertise in FEM enables us to conduct precise calculations at an early stage, such as fluid flow simulations, modal analysis, and thermomechanical calculations. This allows us to optimize the durability, safety, and efficiency of our products during the development phase.
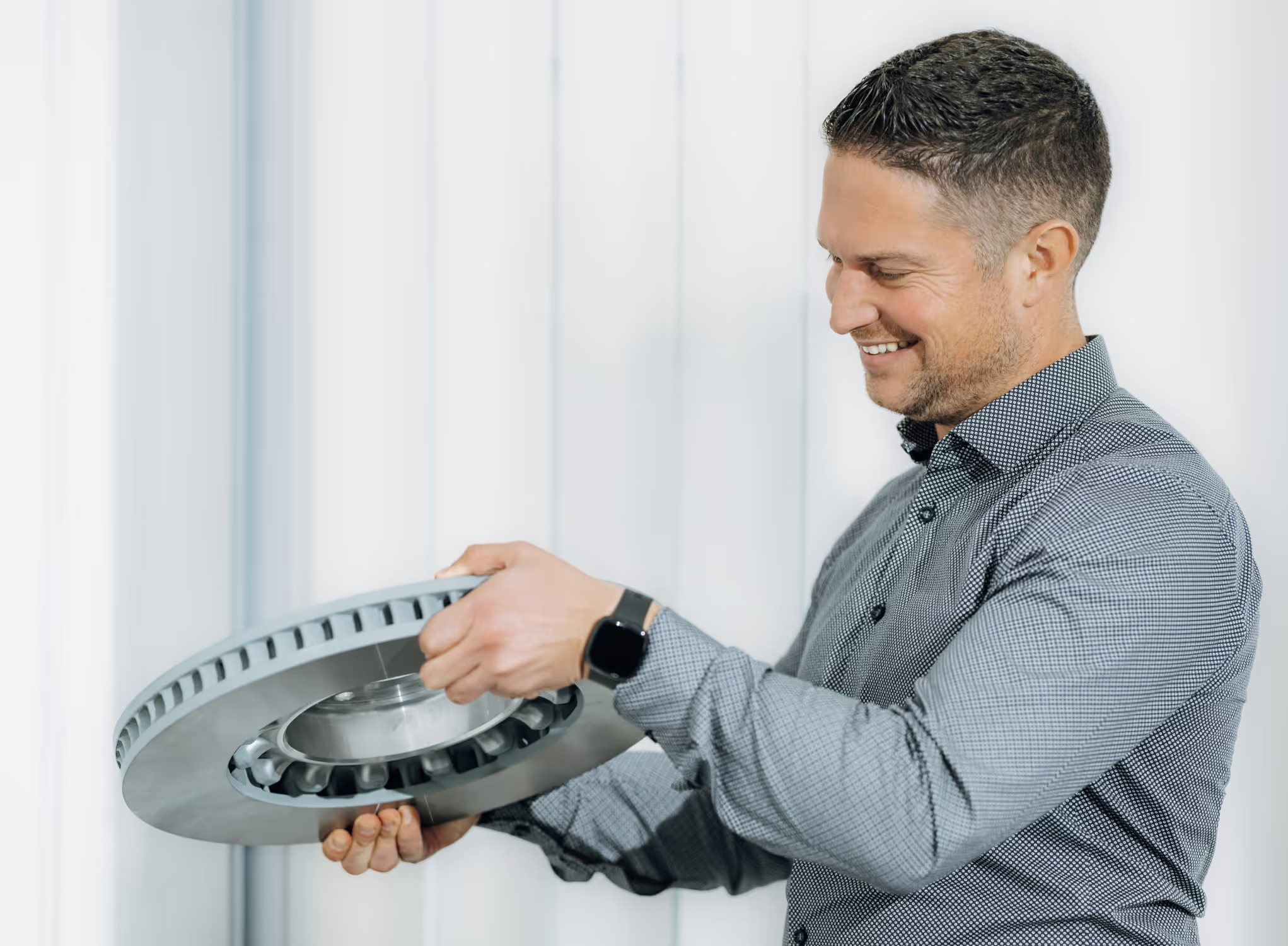
Prototypes
Already close to series production
Successful prototype manufacturing is a critical factor in our product development process. Thanks to our in-house production capabilities, we can quickly and precisely turn ideas into high-quality prototypes. From the very first concept phase, prototypes are produced at Breyden using processes close to series production, allowing us to react flexibly to changes and ensure the highest quality standards. This enables us to achieve short development cycles and continuously optimize our products, even before they enter serial production.
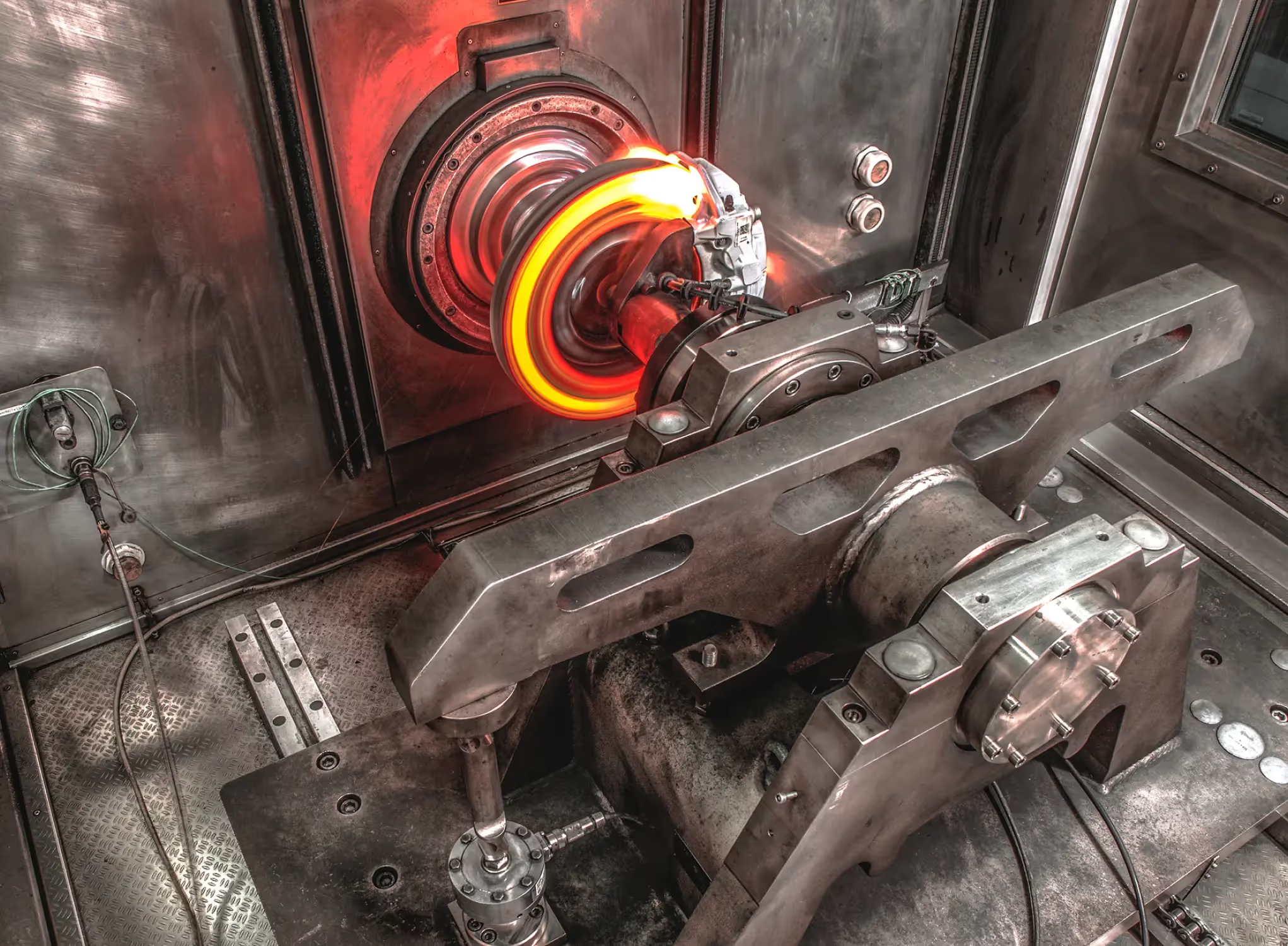
Dynamometer Test
Standardized to customized brake tests
Breyden has brake performance test stands that enable component testing of disc brakes for passenger cars and light commercial vehicles. To simulate environmental influences in real-world operation, we can condition both ambient temperature and humidity. Additionally, we can simulate the extra load on brake discs in winter conditions, including exposure to corrosive media. A test chamber is also available for testing components based on standardized norms (e.g., DIN EN ISO 9227, 11997-1, 6270-2, or VDA 621-415). Thermal analyses can be conducted using specialized thermography equipment. Standardized brake tests such as AK-Master, crack formation, deformation, high load and wear are possible, as well as customized testing procedures based on customer requirements.
Project Management
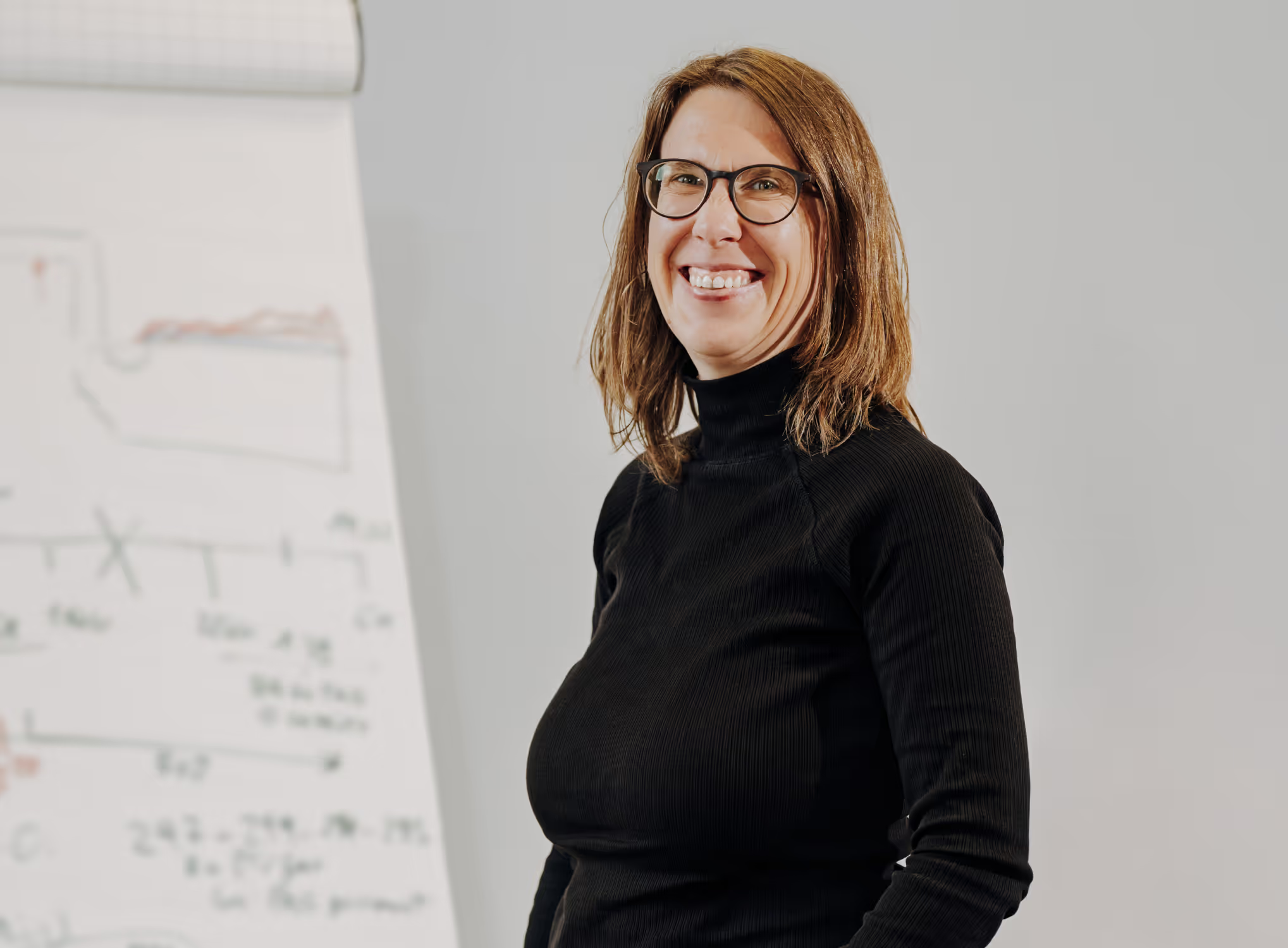
Success through defined processes
The Key Factor
A structured approach to planning, execution, monitoring and completion of projects is an essential element for the success of our projects. Therefore each of our projects is carried out according to a clearly defined milestone plan. Key elements include communication, regular updates and clear reporting to keep all stakeholders informed and to identify and resolve potential conflicts early. Through our professional project management, we have the ability to respond to changes and adapt to new requirements. This is a crucial factor for the success of our projects.
Serial Production
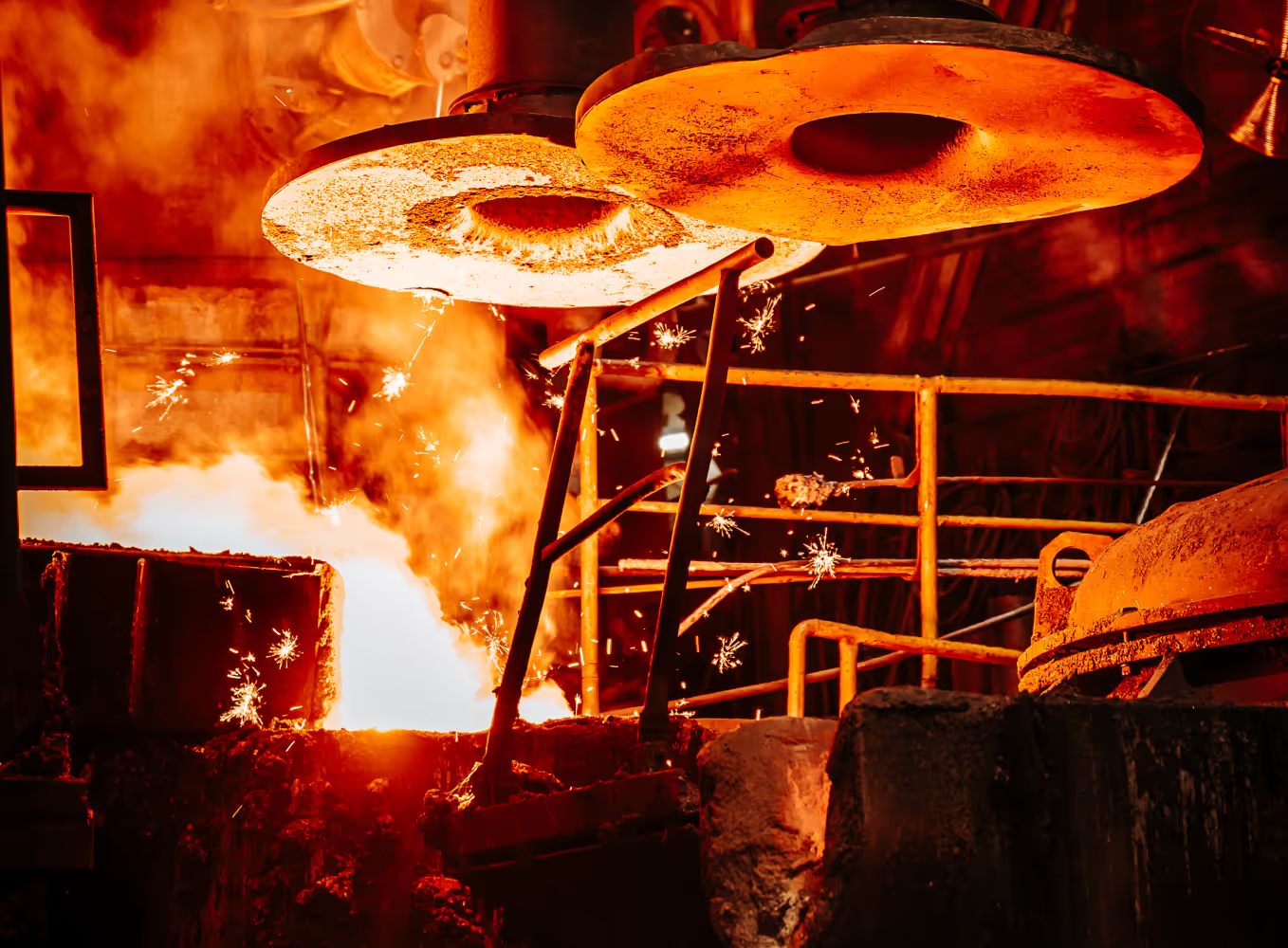
Foundry
On the way to the green foundry
Breyden produces brake discs that meet the highest demands of our customers in two foundries on five vertical molding lines. Advanced manufacturing technologies and highly automated processes play a central role in this. Our expertise ranges from the selection of premium raw materials to the precise manufacturing and inspection of the products. Currently the molding lines are supplied with molten iron by a cupola furnace and several medium-frequency furnaces. In the near future the cupola furnace will be replaced by additional medium-frequency furnaces. This is another step closer to our vision of green brake disc manufacturing.
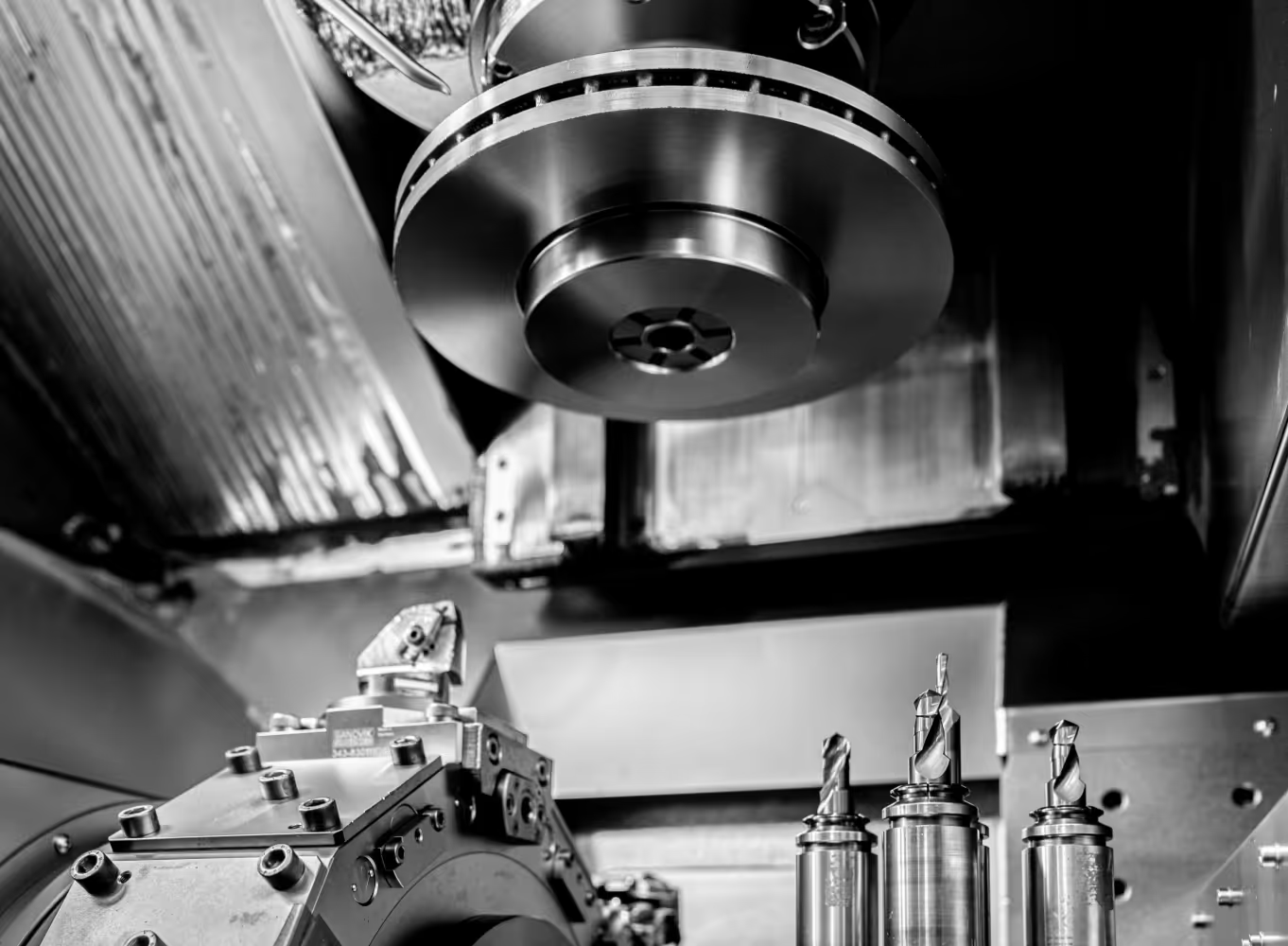
Mechanical processing
High quality and efficiency in brake disc machining
All our brake discs are manufactured with the highest quality on fully linked systems. The final processing is performed either through fine turning or double-disc grinding operations. We internally develop all tools, machining processes, and workflows using the latest methods. Various painting systems are available for the final corrosion protection, efficiently processing different coatings.
.avif)
Hard-metal coating
Pioneer in hard-metal coating of brake discs
With the series launch of the iDisc I in 2017, Breyden became a pioneer in the hard-metal coating of brake discs. While the iDisc I is coated using the HVOF process, the next generation uses the innovative high-speed laser cladding process. This manufacturing method enables us to apply a variety of hard metals to our brake discs. Following the final grinding process, we deliver brake discs to our customers that contribute to meeting the future Euro 7 standards.
.avif)
Rüdiger Mosis,
Head of Development and
Machining for brake discs